Agri-Plastics Custom Rotomolding develops and tests its products through hands-on experience. Our mission is to offer the best quality plastic products by designing solutions that meet our customers’ expectations, while establishing a worldwide reputation for reliability and durability.
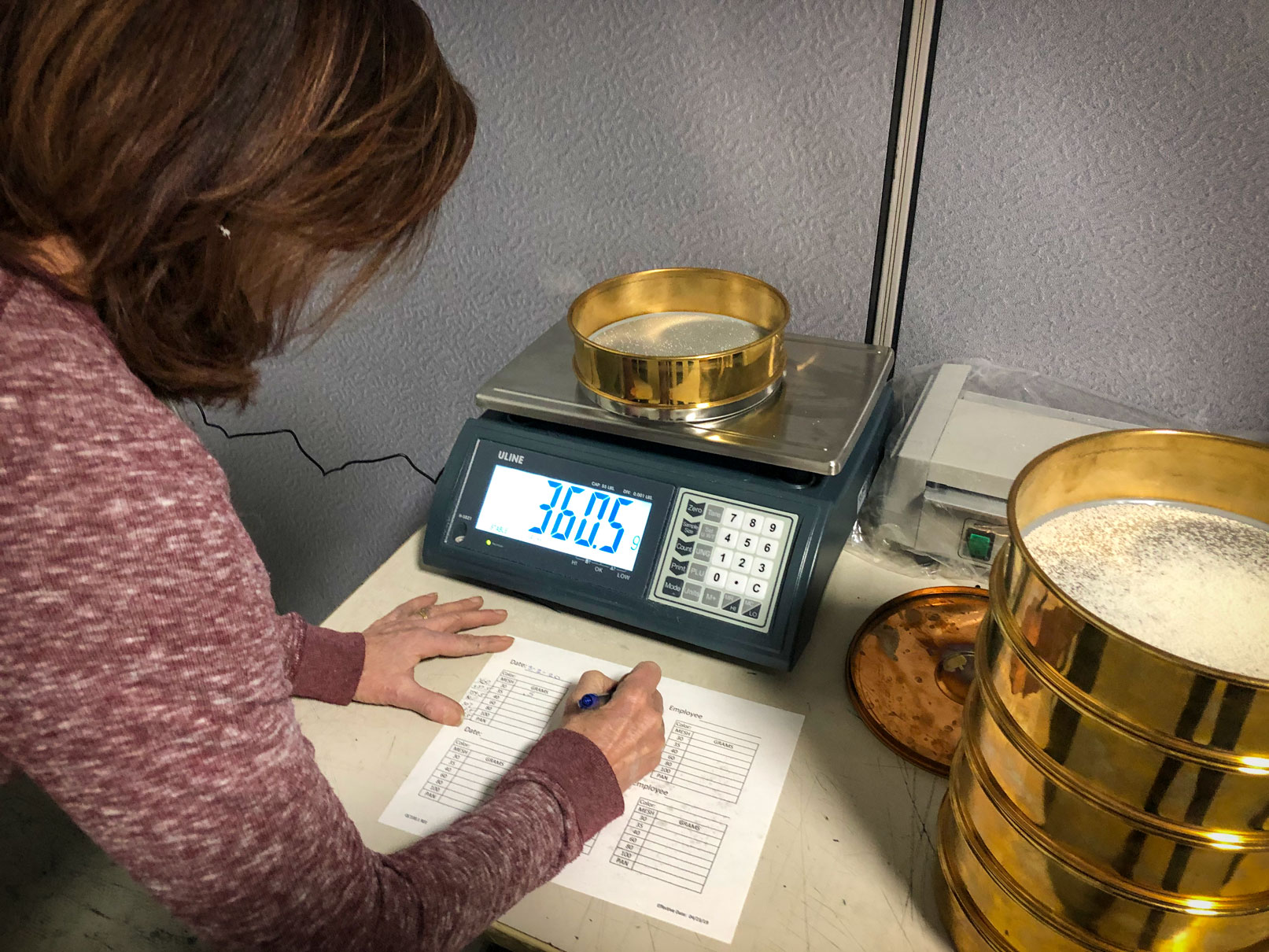
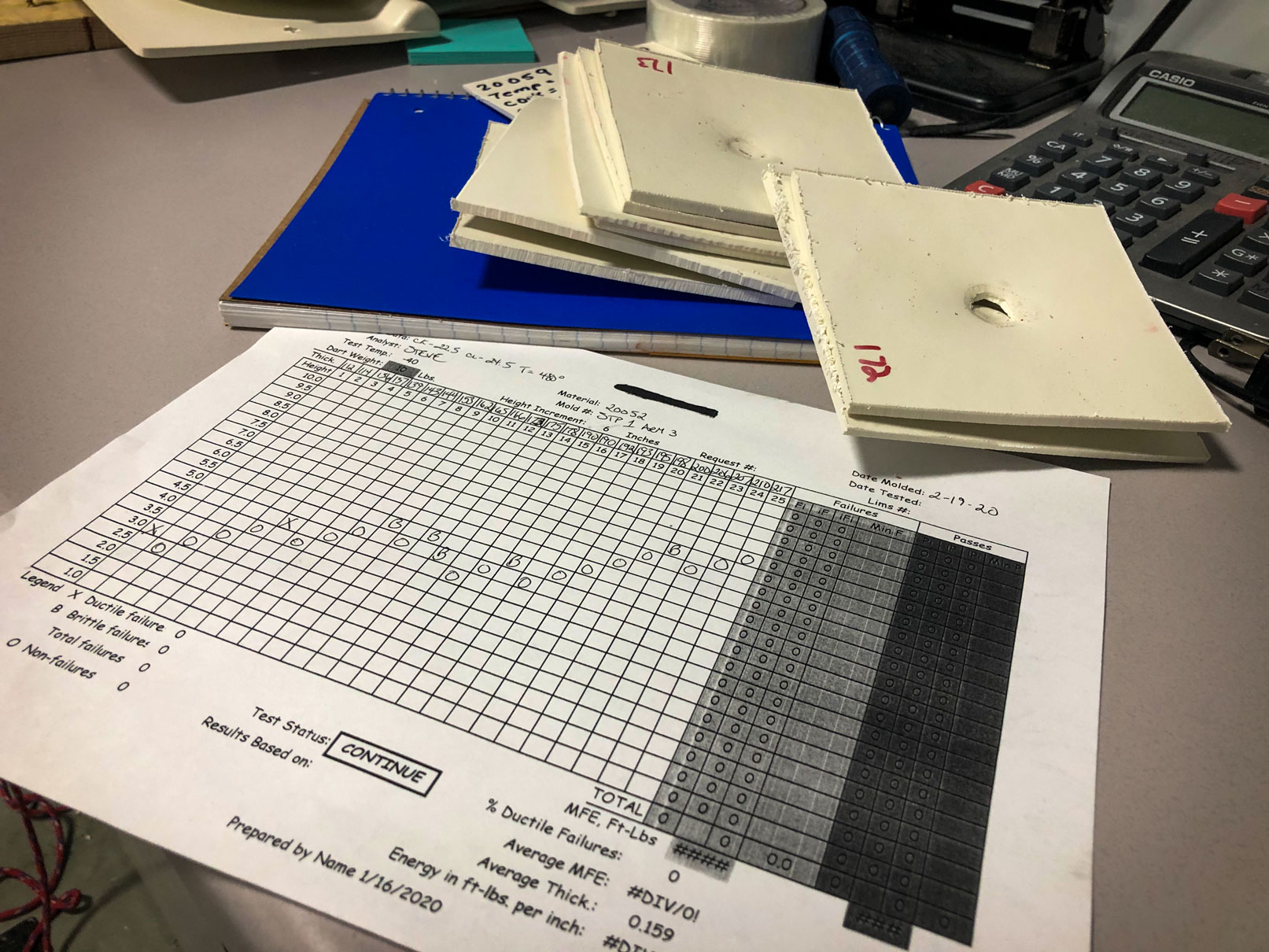
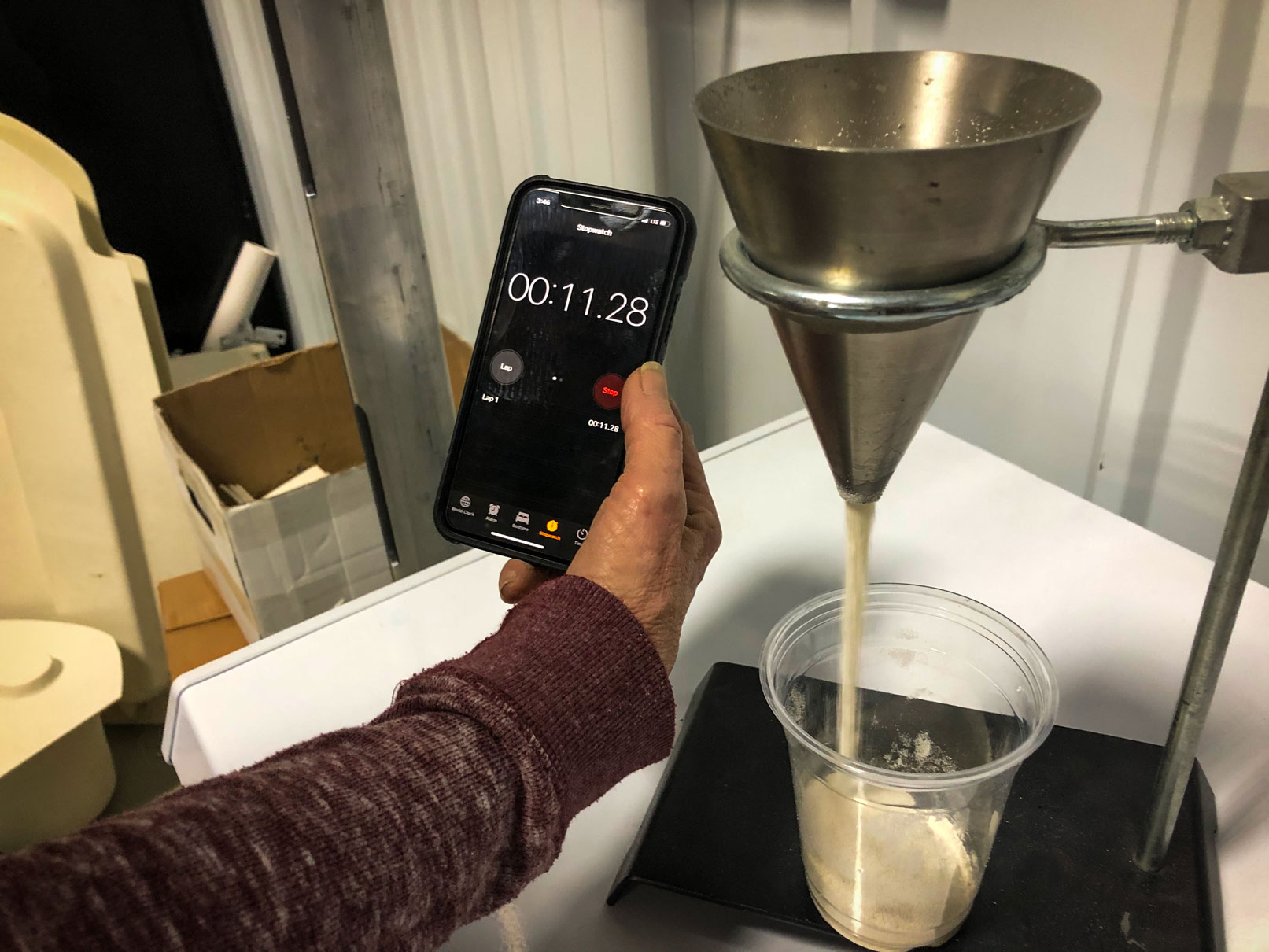